Poor flux cleaning means that the flux used is not completely cleaned or removed after welding. This may appear as traces or residues of flux remaining on the welding area or metal surface. Poor flux cleaning may manifest as the following:Visible residue: Residual flux can be seen on or near the surface of the welded parts. This may appear as a sticky, different color or shiny substance that may adhere to the weld point or other locations in the welding area.Chemical analysis and testing: Residual flux can be confirmed by chemical analysis or testing methods. This may require laboratory testing or special testing equipment to determine the type and amount of residual material.Impact on welding points or product performance: Poorly cleaned flux may affect the quality and stability of welding points. This may cause the electrical or mechanical properties of the welding point to deteriorate, and may even cause failure or poor connection.Appearance impact: Residual flux may affect the appearance of the product, which may make the welding part or the overall product look unclean or not meet the appearance requirements.What can the problem of unclean flux cleaning cause?
Circuit board contamination: Uncleaned flux may leave residue on the surface of the circuit board, causing circuit board contamination. This may affect the performance and stability of the circuit board, causing circuit failure or short circuit.Corrosion and oxidation: Flux residue may contain chemicals that may cause corrosion or oxidation if left on the circuit board or soldered parts for a long time. This may reduce the life of the parts and damage the performance of electronic components.Weak soldering: Uncleaned flux may prevent good connection of solder joints. It may form isolation materials around the solder joints, resulting in weak soldering or poor contact.Appearance impact: Flux residue may affect the appearance of the product, which may cause the appearance to be unclean or not meet the appearance requirements.Performance issues: Flux residue may have a negative impact on the performance of the device. For example, components such as sensors, resistors or integrated circuits may not work properly due to the presence of residues.Why does the problem of unclean flux cleaning occur?01Residue characteristics: Some fluxes may have special chemical properties that make them difficult to clean thoroughly. Some fluxes may not be easily dissolved or removed during regular cleaning, requiring stronger cleaning agents or special cleaning methods.02Improper cleaning methods: Using inappropriate cleaning methods may result in poor cleaning results. If the cleaning agent or cleaning process is not sufficient to effectively remove the flux, incomplete cleaning will occur. Sometimes multiple cleanings or changing to different cleaning agents may be required to achieve better results.03Inadequate cleaning equipment or processes: Cleaning equipment or processes may not be sufficient to handle specific types of flux residues. For example, some fluxes may require special cleaning processes such as ultrasonic cleaning or spray cleaning, while simple manual cleaning may not completely remove the residues.04Time and resource constraints: Sometimes in a production environment, time and resource constraints may lead to neglect or simplification of cleaning steps, resulting in incomplete cleaning.SolutionIJING SJ-09A
A pH-neutral water-based cleaning agent designed specifically for power electronics and PCBA cleaning can quickly and effectively remove different types of post-solder flux residues.Case sharingThe end customer's existing online spray cleaning process is completed using a water-based cleaning agent. The new process that the customer wants to launch needs to consider the sensitive materials on the surface of the substrate. Based on the requirements of the new process for material compatibility, our company discussed and selected a pH neutral water-based cleaning agentExperimental designThe customer prepared 2 different tin-coated PCBA tests, both of which were uncleaned double-sided assembly boards, and there were also fixtures. The cleaning equipment used was an online spray cleaning equipment.
Visual inspection resultsAfter cleaning with the above process parameters through the online equipment, all substrates and panels can be cleaned at one time. See the comparison before and after cleaning in the figure below.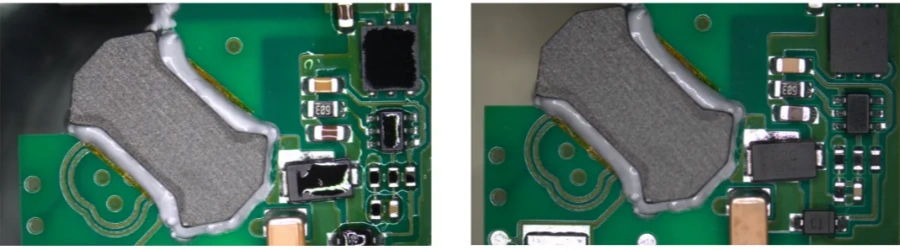
Figure 1 Before cleaning (left) and after cleaning (right)
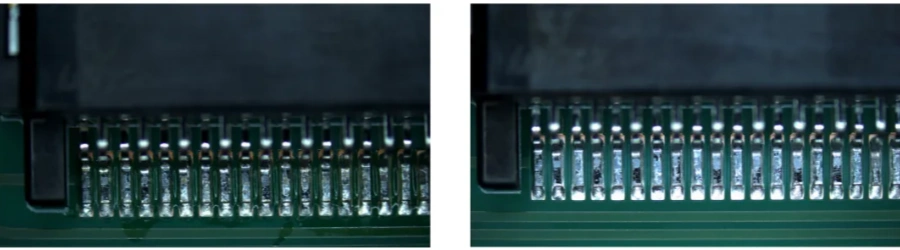
Figure 2 Before cleaning (left) and after cleaning (right)
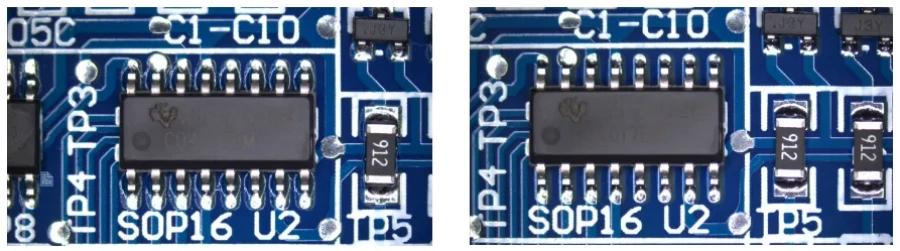
Figure 3 Before cleaning (left) and after cleaning (right)
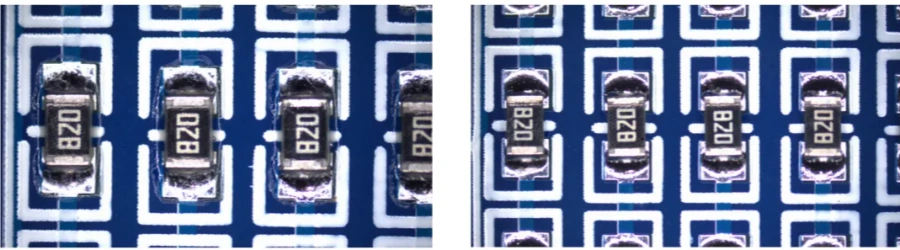
Figure 4 Before cleaning (left) and after cleaning (right)